Interview with Richard Edelman, manager of logistics
How long have you worked at MTEE?
I started my career at MTEE in September 2013, so I have worked here for seven years. I started in the same role as I am in now, namely manager of logistics. Two years ago, I was also assigned as project leader for the implementation of SAP for the turbo division.
What is your background?
Including my time at MTEE, I have more than 20 years of experience in logistics and operations management. I have worked with two different logistics companies and two trading companies. This means that my logistics focus back then was on road transportation and general logistics. At MTEE, my focus lies within internal logistics and production logistics. My department is responsible for warehouse administration, replenishment of parts to and from our production lines and warehouse expedition.
How has the logistics department evolved over the years?
Just before I came to MTEE, one of the biggest changes in logistics was already made: the EV-train concept of replenishment. Before this, all parts were stored in our warehouse and brought to the production lines using forklifts. The packing units were stacked to the ceiling. Now, a small EV-train brings the parts to the assembly lines “just-in-time”. Furthermore, the parts are stored in an external warehouse operated by the company Jan de Rijk, right next to MTEE. Where we also used to make the parts available just outside the production area, we now have a logistics team inside the production lines as well. The train employee from Jan de Rijk brings the parts outside the factory and our logistics employee scans it inside and brings it to the production line. This clear line of responsibility makes it easier to improve and makes the process more transparent.
Based on kaizen, another change made was the replenishment of bulk parts. Bulk parts are now replenished in a KIT-car containing all the necessary bulk items for the shift to come. This makes the process a lot more efficient for the line operators. It is also our job to make sure that these are replenished on time.
We also took on the responsibility of customer logistics. This means that we deal with both the customer and the transportation company of the customer. Based on the customer’s EDI, we make sure that the requested turbochargers are ready for pick-up.
What influence has Six Sigma had on the logistics department/production?
I have always been interested in improving existing processes. I received my first Six Sigma training in the early 2000s I have learned to use that and later on the Lean tools. Where Six Sigma is focused on reducing process variation, the Lean Tools are focused on increasing value to our product/service in the eyes of the internal customer.
I have been involved in many improvement projects at MTEE – some small and some large. The most important ones are:
- Reducing and/or avoiding production line stops with more than 50%.
- Reducing and/or avoiding damages in the JdR warehouse. We managed to improve by more than 70%.
- Productivity improvement of the bulk-part replenishment. We managed to do the work with fewer people.
What are the everyday challenges in turbocharger logistics?
I would say first of all it is inventory accuracy. The motto of the logistics department is to make sure that the physical stock situation is equal to the administrative stock situation. So we do all that we can to always have a real-time accuracy of the stock and so prevent the worst case scenario: a line stop due to lack of parts. In an ideal world, there is no rework and scrap. However, this is where the inaccuracies lurk. Supported by the ERP system, we have a wall-to-wall stock count two times a year to ensure that any difference is corrected.
The second greatest challenge is to manage and monitor the warehouse capacity. When I started at Mitsubishi, we produced around 2.5 million turbochargers a year. In the last couple of years, we have produced more than three million per year. If you see this volume increase, and do not take action, it might not fit in our warehouse. Therefore, it is important to become aware of these changes ahead of time and take responsibility.
A great part of managing the warehouse capacity is also traceability. We need to makes sure that every step of the logistics process is validated with our scan system. Every time we have an inbound shipment, we print labels for every box, thus providing a unique time stamp. This way we know exactly when it arrived and we know, based on “first in, first out” principles, exactly which parts should be used first. Every time a batch of parts is brought to the production line, we scan it. If something should go wrong, we can always look back in the process and find out where it happened.
What effect has Covid-19 had on logistics?
The greatest effect was probably the decrease in production volume. We had a lot of customers who shut down their factories temporarily, which meant that we only needed to produce a fraction of what we normally do. For around three weeks we had to let the temporary line operators off. This left us with only our own team – logistics, which meant that employees who don’t normally work as logistics operators would support in the production with line feeding. When there was a drop in volume, we kept on producing for backorders. Around mid-May, we saw the volumes improving, and we have weeks where we are back to normal again. I am really impressed with how flexible my team members and everyone else have been in supporting these challenges. After three weeks, the first temporary workers came back again.
As for our suppliers, we saw signs ahead of time that some of them would be affected by the crisis. We have a number of Indian and Italian suppliers, for instance, who had to shut down temporarily as well. In February, when we saw the first signs, our planning department made some large orders to make sure we would have enough stock. However, when many of our own customers also stopped production it decreased the stress on MTEE and logistics.
How do you see the logistics department developing in the future?
The future of logistics is all about efficiency. We recently replaced BPCS – our former ERP system – with SAP as BPCS had become outdated. We had to say goodbye to a system that was working, and with which we all knew the procedures very well. It is a big transformation, but ultimately SAP will increase the efficiency of our company.
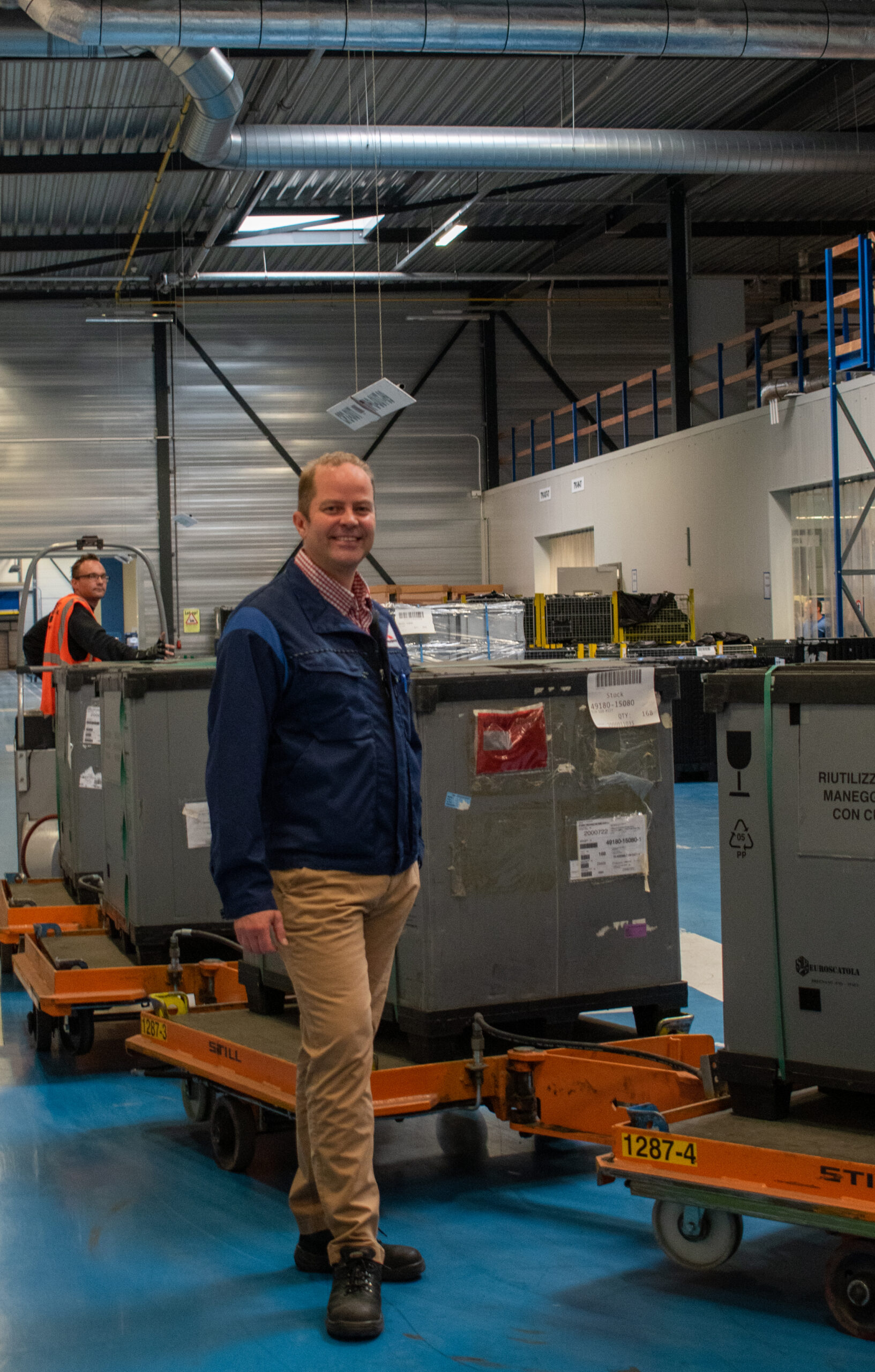