Turbochargers are built to last the lifetime of a vehicle. Car manufacturers extensively test the uniquely matched turbocharger and engine together, to avoid any unexpected failures. However, lack of maintenance, hazardous driving or a single component failure, could have a harmful influence on your turbocharger. In this post, we will look at the 5 most common reasons that your turbocharger could fail.
Foreign object damage due to hitting by larger metal fragments
1. FOREIGN OBJECT DAMAGE
Turbochargers move at rotational speeds higher than 200.000 RPM (over 3300 rotations per second!). You can imagine that at those speeds, damage accumulates incredibly quickly. Since the tips of the blades move at a speed of around 2000 km/h, any object that enters the turbochargers, even as small as grains of sand, can damage a turbocharger enough to make it perform incorrectly or fail instantly. As protection, the manufacturer will design and install an air filter to prevent objects from entering the turbocharger so that this kind of failure does not happen often. However, if an object should enter the turbocharger from the engine side, like for instance a part of a piston ring, it will not be caught by any filter. If this occurs, you will feel an immediate drop in engine power or the engine will stall completely. The turbocharger will have to be replaced in this case.
TIP! By regularly checking your air filter, to make sure it is in good condition, you can prevent any objects coming in from the outside and potentially damage your turbocharger. It is a little more difficult to prevent foreign object damage caused by particles coming from the engine itself, except from making sure that the engine is regularly checked by a professional.
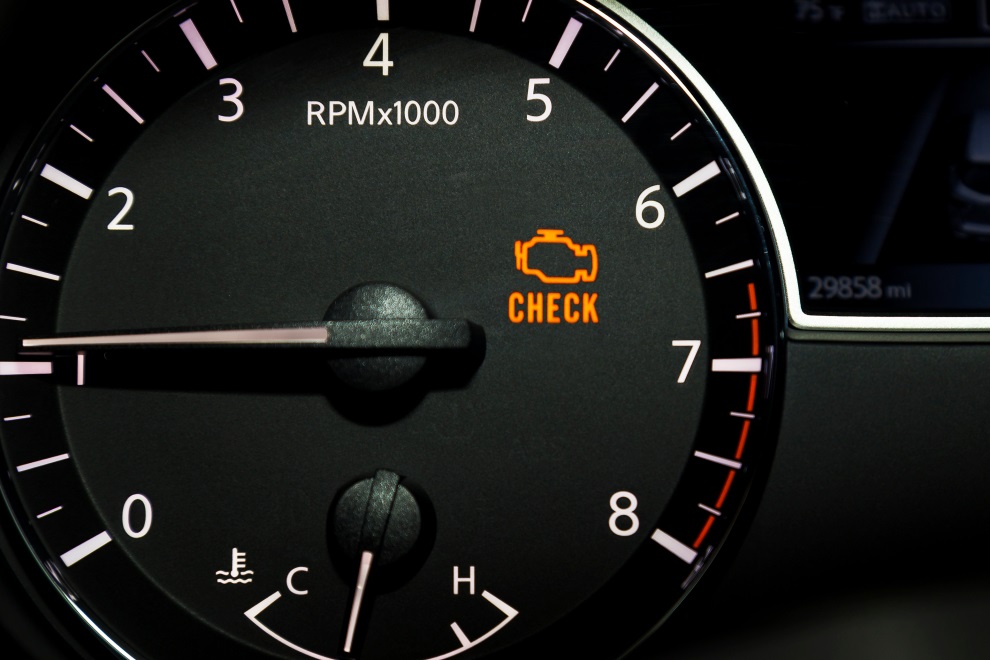
2. STICKING
At MHI we design and produce turbochargers with two different types of control systems; a W/G (waste gate) turbocharger and a VG (variable geometry) turbocharger. Both systems are used to control the turbocharger behavior and speed. If either one of the systems gets stuck, you might experience the following symptoms: If the W/G or VG system is stuck in a relatively open position you will experience a lack of performance. This is caused by a part of the exhaust gasses being bypassed in a W/G turbo or not enough pressure build up in a VG turbo and therefore not being able to deliver the desired boost to the engine. In this case the car will not accelerate as quickly as you are used to. If the W/G or VG system is stuck in a relatively closed position you will see your engine light in the dashboard turn on. W/G or VG systems in a turbocharger are there to control the amount of boost delivered to the engine. If this system fails, the engine will detect it is getting too much boost. To protect itself, the engine will turn on the light on the dashboard and might also go into limp mode. An important thing to note is that a W/G system has a tendency to get stuck due to corrosion and a VG system has a tendency to get stuck due to contamination.
TIP! A relatively simple thing you can do as a driver to keep both systems moving is the following:
- Use the car regularly, this will not give corrosion or contamination a chance to settle and increase the friction in the system or get it stuck completely.
- Use complete engine range. This has two benefits: Firstly, if you use the full range of the engine RPM and engine power it has to use the full range of the W/G or VG system as well. This makes sure that the system remains operable in full range. Secondly, the heat generated at higher engine loads can help in burning away part of the contamination that might have built up on the system.
Of course, if you do these things make sure that the engine is on operating temperature and make sure that you don’t give the car a hot shutdown (see Heat Soak below for more information).
3. BEARING WEAR
The most sensitive components of a turbocharger are its bearings. With tolerances smaller than the thickness of your hair, even the slightest imperfection can cause it to fail over lifetime. There are 2 types of bearings in a turbocharger: a radial bearing (left) and an axial bearing (right).
Both photos show a large amount of bearing damage due to oil starvation
The radial bearing supports the side-to-side movement of the shaft of the turbocharger. The axial bearing supports the axial movement of the shaft. Both bearings are very dependent of the oil supplied to them. If the oil quality (particles in the oil) is bad or not enough oil is supplied, failure of the turbocharger can happen within seconds.
TIP! Always stick to the prescribed oil change intervals.
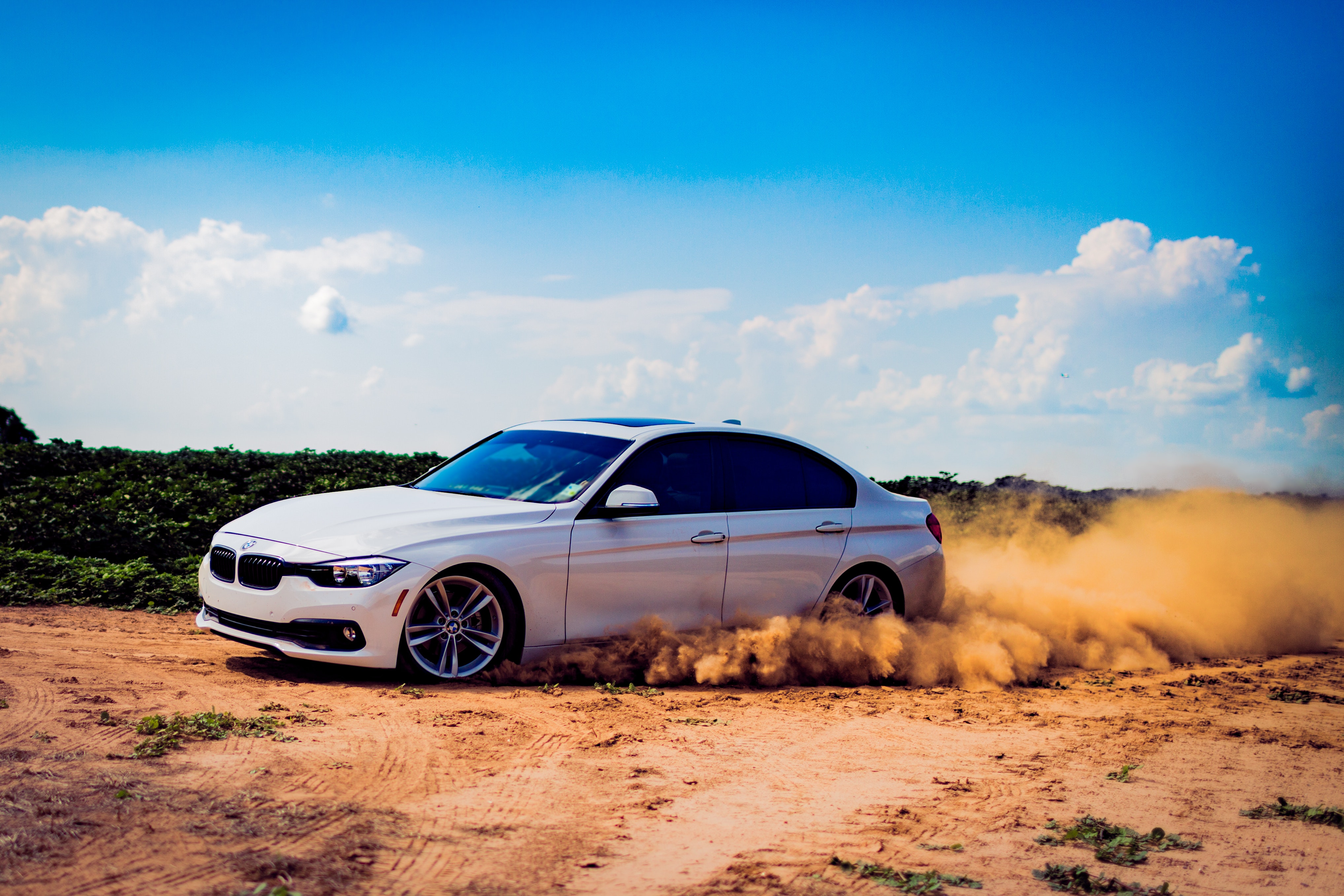
4. SURGE
A turbocharger forces extra air into the engine to be able to burn more fuel. In the industry, the compressed air is called boost. If you want to accelerate, boost is necessary. There are also scenarios when the turbocharger is still providing boost, but the engine does not need it. For example, when you shift gears. At this point the throttle valve closes. The turbocharger is however still rotating very quickly and is still building up boost. Due to the closed throttle valve this boost cannot be delivered to the engine anymore and the boosted air accumulates in the inlet manifold. When the amount of accumulated air becomes too much, it will start flowing backwards into the wrong direction over the compressor wheel. After this “release” the compressor wheel will again build up boost and the cycle repeats. This pulsating air flow is called surge and can be quite violent and puts a lot of stress on the bearing system, the shaft and the compressor wheel. Prolonged exposure to surge can lead to catastrophic failure of the turbocharger.
TIP! There is unfortunately not much you can do as customer to prevent surge. If you believe that your engine is running irregularly, please take it to your dealership.
5. HEAT SOAK
Turbine rotor with oil coking on the bearing and shaft
The fact that a turbocharger works in a very hot environment already poses challenges of its own during operation. Sufficient cooling is needed to keep everything (primarily the bearings) functioning correctly. Something inevitable during driving is eventually turning off the engine. Sometimes this occurs after the engine has been working hard with all the components being very hot. These so called “hot shutdowns” (sudden engine shutdown after period of high engine load) pose another potential risk for failure of the turbocharger. During operation there will be plenty of oil and coolant going through the turbocharger to keep all temperatures within the designed limits. However, when the engine is shut off quickly after a high engine load situation the flow of cool oil and coolant stops. This will cause the remaining oil in the turbocharger to “soak” the heat increasing the likelihood of oil coking which means that the oil will burn and leave particles in the bearing system and on the shaft. This will damage the bearings and the cartridge could become noisy due to this.
TIP! During development of the engine the OEM’s test for heat soak. They can also implement independent pumps to keep oil and coolant running for a while after the engine is shut down. This will significantly reduce the heat soak and lower the chance of oil coking. If you have an older car with a turbocharger, it will help to account for this as a driver by driving less aggressively (no high loads on the engine) for the last few minutes before shutting down the engine to lower the risk of oil coking due to heat soak.